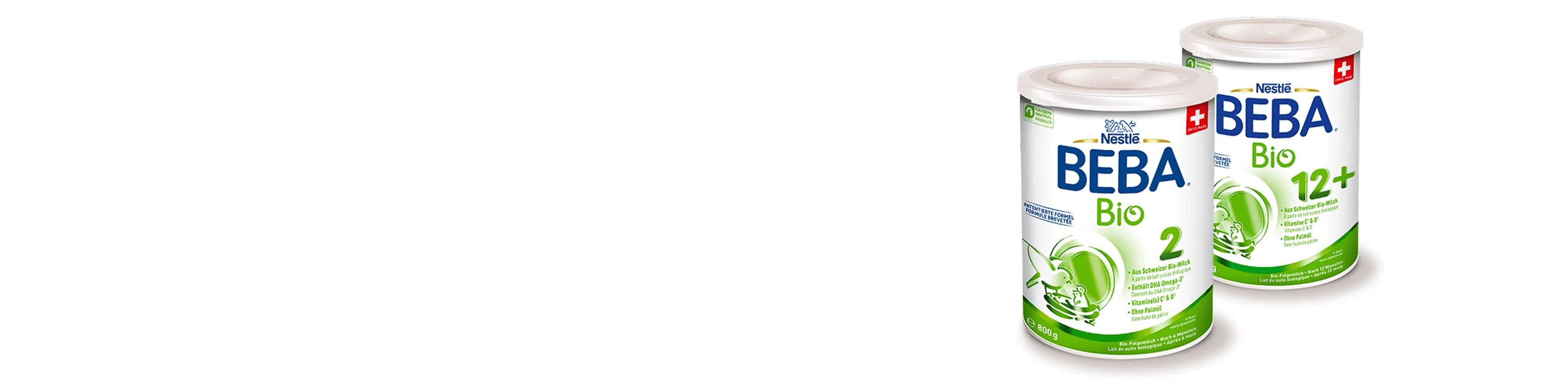
Nestlé Suisse S.A., Konolfingen
Reprogramming of Existing UHT Systems
The existing three UHT systems have always had the disadvantage that they were not implemented with a Nestlé Automation Framework, but in the supplier's standard. Troubleshooting and functional enhancements were therefore always very limited. We were now able to completely reprogram the systems. A lean, comprehensible PLC code in the Nestlé framework allows a complete understanding of all processes for the first time. Additional requirements could now finally be met. The systems are also fully mapped in the visualization. Commissioning was carried out in just a few days so that the entire line had minimal downtime.
Line Management System
Extension of a line management system to two new production lines and coordination of interfaces with suppliers
Replacement of MES Probiotic Factory
MES migration of a complete production line. Connection of the PLC routines and structures to the MES system, preparation and processing of signals and data in the PLCs, integration of the GUI in existing HMI applications, configuration of the MES objects.
Capacity Expansion Probiotic Factory
Expansion of a liquid production line to increase capacity. Integration of additional tanks into the existing plant.
Milk Reception MES Replacement
The existing liquid reception MES was replaced with Nestlé's own DMO system. Our task was to configure DMO, which was developed by a third-party company, and to make all the necessary adjustments in PLC and HMI. In the process, some things were simplified and harmonized, certain processes were adapted to today's use and operation was fundamentally simplified.
BMOS DMO Implementation
Connection of a new plant part to an existing MES system.
BMOS Dissolving and Storage
Section of a plant for the dissolution of various powdered ingredients, storage of the solution as well as continuous liquid dosing into the downstream process.
CIP2 Extension
An existing Cleaning in Place (CIP) station was extended. In several phases, all electrical elements were renewed. Then several cleaning circuits were transferred from an older cleaning station to this system. The main challenge was the integration into two systems with different control and HMI generations. Finally, the interruptions for rebuilds and commissioning were always relatively short.
IBC Cleaning Station
Up to now, the cleaning of the intermediate bulk containers (IBC) for powder was carried out in laborious manual work. Here, a system was developed, in which the IBCs are vacuumed from the inside by means of a robot arm. The Fanuc robot was programmed by a subcontractor. Our work included the procurement of the control cabinet, the integration of the robot, various safety elements, an extraction system as well as the entire operation and integration into the factory's control system.
Adjustable Spray Nozzles on Spray Dryer
A special nozzle was developed by Nestlé Research for the controlled regulation of the product injection in the spraying tower. In various preliminary projects, we were allowed to develop the software for the control of these nozzles. In this project it was now possible for the first time to use it in the industrial environment on production line 2 of the factory. The challenge here was the synchronous control of several servo motors in an environment with high temperatures and under high product pressure.
Line 2 Powder Handling after Spray Dryer
For the new production line 2, the powder transport after the spray drying tower was automated. By means of pneumatic senders, the powder reaches the various destinations, such as Big Bag or IBC filling stations.
Line 2 Oil Handling
For the New Wet Line production line, the oil dosing for oil mix and LC-PUFA was automated.
Line 2 Dissolving
For the New Wet Line production line, the liquid part from milk and cream storage tanks to dissolving and inline dosing was automated.
Line 2 Wet Mixing
For the New Wet Line production line, the following plant sections were automated: Big Bag Tipping, powder conveying and storage, and dosing of the powder into the liquid section.
Standardised Powder Mixing
Based on the standardized solution for high-precision dosing and mixing of baby milk powder, a variant of the software for Gericke's equipment was developed for the new construction of four mixing lines.
Phoenix Liquid Line
Complete automation for the liquid part of a new production line. Deleproject was responsible for the automation, including control cabinet construction, for the plant parts standardization, dissolution and inline dosing.
Phoenix Powder Line
Complete automation for the powder part of a new production line. Deleproject was responsible for the automation, including control cabinet construction, for the plant sections big bag tipping, powder conveying and storage, dosing into liquid process and spray drying tower, transport after the spray dryer, and dry mixing.
Phoenix Milk Reception
In close cooperation with the plant manufacturer (client), the control cabinet manufacturer and the end customer, the automation for several milk and oil reception stations, storage tanks and milk processing (separation) was developed. A CIP station was also part of the order.